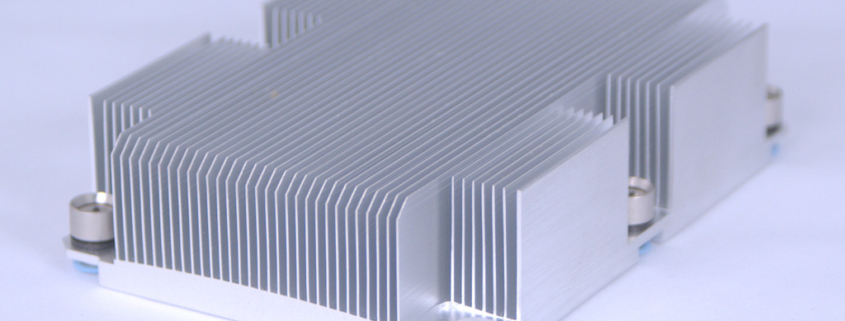
A cylindrical aluminum block is heated to high temperatures (about 480°C) in a forge. Then, it is placed on a loader, and pressure is applied with a punch to push the heated aluminum through the die.
After that, it was stretched in the die cavity shape. The finished extrusion is then cooled and straightened, and, if necessary, hardening produces the finished product.
This can be cut to the desired lengths, drilled, and machined.